一、引言
冷冻干燥作为一种通过升华去除水分的先进技术,广泛应用于生物制药、食品加工、材料科学等领域。然而,实验过程中常因工艺参数不当、设备操作失误或样品特性差异导致冻干失败,表现为产品塌陷、活性丧失、含水量超标等问题。本文结合实验室冻干机的实际应用场景,系统性梳理10个常见故障的成因与解决方案,并提供可操作的优化策略。
二、常见冻干失败问题与根因分析
1.冰晶形成与结构破坏
现象:
样品内部或表面出现明显冰晶,升华后导致蛋白质变性、细胞破裂或复溶率下降。
根因分析:
预冻速度不足:缓慢冷冻时,溶液未通过玻璃化转变(Tg),形成大冰晶,刺破细胞膜。
共熔点(Tm)控制偏差:冷冻温度高于样品共熔点,导致部分液态水残留,升华时形成二次冰晶。
解决方案:
快速预冻技术:采用液氮喷淋或快速降温系统(如-196℃液氮预冻3-5分钟),使样品迅速通过Tg进入玻璃态。
优化预冻温度:通过差示扫描量热法(DSC)测定样品的Tm,预冻温度需低于Tm至少10℃。
2.产品塌陷
现象:
冻干后制品失去原有形状,质地松散或收缩成团。
根因分析:
主干燥阶段温度过高:导致冰晶融化或未升华的“假性干燥”。
支撑结构不足:样品浓度过低或缺乏骨架蛋白(如明胶)。
解决方案:
分段控温策略:在主干燥阶段采用阶梯式升温(如-50℃→-30℃),避免局部过热。
添加赋形剂:如甘露醇、海藻糖或明胶,增强样品结构稳定性。
3.复溶率低或活性损失
现象:
冻干产物难以溶解,或关键活性成分(如酶、核酸)失活。
根因分析:
预冻过程中热应力:冰晶机械损伤导致生物分子结构破坏。
干燥终点判断失误:残余水分未降至安全阈值(如≤5%)。
解决方案:
改进预冻工艺:结合超低温预冻(-196℃)与冷冻保护剂(如甘油、BSA)。
精确控制终止条件:通过压力监测(如当真空泵电流下降10%-15%时停止)或KarlFischer水分测定仪确认终点。
4.颜色变化或化学降解
现象:
冻干产物出现黄褐色变色或氧化反应产物。
根因分析:
氧化作用:样品暴露于氧气中导致酚类物质、多酚氧化酶等氧化。
美拉德反应:高温干燥引发氨基酸与还原糖的非酶褐变。
解决方案:
充氮保护:在冻干腔体中注入惰性气体(N₂)隔绝氧气。
降低干燥温度:将主干燥阶段温度控制在-40℃以下,抑制热解反应。
5.含水量超标
现象:
最终产品水分含量超过行业标准(如药品≤3%,食品≤5%)。
根因分析:
干燥不完:真空系统泄漏或温度设置不合理。
二次吸湿:冻干完成后未及时密封包装,导致吸湿返潮。
解决方案:
严格密封包装:使用铝箔袋+干燥剂+氧气透过率(O₂)阻隔层。
验证干燥终点:采用热重分析法(TGA)或残余气体分析仪检测水分。
6.真空泄漏与压力波动
现象:
冻干过程中真空度骤降,压力曲线异常波动。
根因分析:
设备密封性差:真空泵油封老化、腔体法兰未拧紧或冷凝器管路泄漏。
冰堵现象:未全部升华的水蒸气在冷阱中结冰,阻塞气流。
解决方案:
定期维护设备:更换真空泵油封(每500小时或1年一次),检查密封圈弹性。
预冷冷阱充分:冷阱温度需提前降至-60℃以下,避免水蒸气凝结堵塞。
7.能耗过高与运行成本上升
现象:
冻干周期延长,电费或液氮消耗量显著增加。
根因分析
真空系统效率低下:油封式真空泵功耗高,或冷阱捕集能力不足。
工艺参数不合理:预冻时间过长或升华速率过慢。
解决方案
升级真空系统:采用干式真空泵(如SPX真空泵)或磁悬浮高速泵,节能效率可达30%。
优化升华速率:通过增大加热面积(如铝制托盘)或提高腔体真空度(≤5kPa)加速水分去除。
8.控制系统不稳定或数据异常
现象:
温度/压力传感器读数漂移,PID控制失效,导致工艺失控。
根因分析
传感器校准偏差:长期使用后传感器灵敏度下降。
软件算法缺陷:PID参数设置不合理(如比例带P、积分时间I、微分时间D)。
解决方案
定期校准设备:每季度对温度、压力传感器进行NIST标准校准。
自适应控制算法:采用模糊逻辑控制(FLC)或模型预测控制(MPC)替代传统PID,提升响应速度。
9.样品污染风险
现象:
冻干机内微生物滋生,导致样品交叉污染。
根因分析
清洁不到位:腔体内残留有机物或微生物孢子。
灭菌不达标:蒸汽灭菌(SIP)或紫外线消毒未能杀灭所有微生物。
解决方案
执行SOP清洁程序:使用75%酒精擦拭内壁,高压气体吹扫管路。
强化灭菌措施:采用过氧化氢汽化灭菌(VHP)或高温等离子体灭菌技术。
10.材料兼容性问题
现象:
冻干机内壁或样品容器发生腐蚀、变色或吸附作用。
根因分析
酸性/碱性样品腐蚀:如磷酸盐缓冲液(PBS)腐蚀不锈钢内壁。
材料吸附活性成分:塑料容器释放单体或增塑剂污染样品。
解决方案
选用耐腐蚀材质:接触强酸/碱的部件改用钛合金或哈氏合金。
优化容器选择:玻璃瓶内壁镀硅烷膜或使用惰性聚合物(如PVDF袋)。
三、案例分析与实战演练
案例1:mRNA疫苗冻干失败(塌陷与活性损失)
背景:某实验室采用传统冻干机制备mRNA疫苗,复溶后病毒样颗粒(VLP)滴度下降50%。
根因:预冻温度(-20℃)未低于样品Tm(-45℃),导致冰晶形成;主干燥阶段温度(-30℃)过高引发结构塌陷。
解决措施:
将预冻温度降至-196℃液氮快速冷冻10分钟;
主干燥阶段分两步升温:-50℃→-30℃,每步保持6小时;
添加5%海藻糖作为保护剂。
结果:VLP滴度恢复至原值的90%,复溶时间缩短40%。
案例2:益生菌冻干粉变色与氧化
背景:冻干后的益生菌活菌数合格,但产品呈现黄褐色。
根因:腔体未充氮保护,残留氧气引发多酚氧化酶褐变。
解决措施:
在冻干前向样品中添加0.1%抗坏血酸抗氧化剂;
冻干过程中向腔体通入95%N₂/5%CO₂混合气体;
包装采用铝箔袋+脱氧剂密封。
结果:产品颜色恢复白色,货架期内活性保持率提高至95%。
四、预防性维护与工艺优化策略
1.设备日常维护清单
每日检查:真空泵油位、冷阱结霜情况、密封圈状态。
每周清洁:用异丙醇擦拭腔体内部,检查加热板温度均匀性。
年度大修:更换真空泵、校准传感器、润滑机械部件。
2.工艺参数标准化
建立冻干曲线模板:根据样品特性固化预冻时间、升华速率、终止条件等参数。
采用QbD理念:通过质量源于设计方法优化工艺稳健性。
3.人员培训与资质认证
操作培训:掌握冻干机原理、SOP流程及应急处理(如真空泄漏报警响应)。
认证要求:实验室人员需通过GMP或ISO13485相关认证。
五、结语
实验室冻干机的成功运行依赖于对设备原理的深刻理解、对样品特性的精准把控以及对工艺细节的持续优化。通过系统分析常见故障的成因并采取针对性措施,结合智能化升级(如数字孪生、AI预测控制),实验效率与产物质量将显著提升。
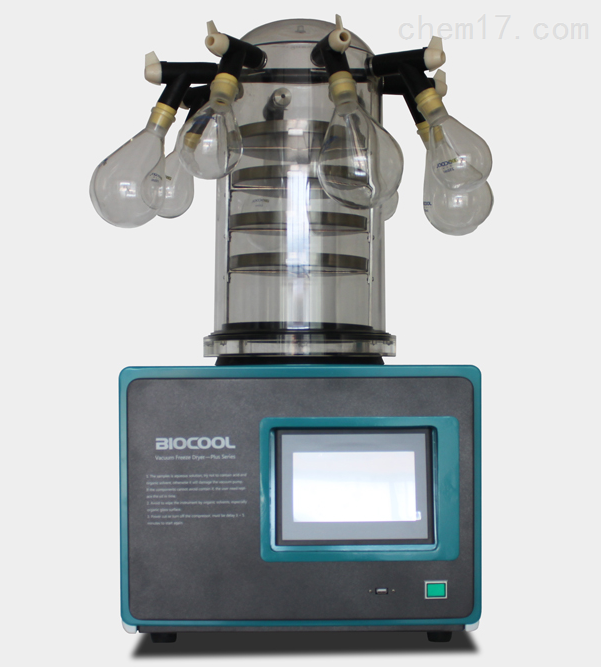